Clean The Surface Of The Plywood
Removing the dust and debris will guarantee that your plywood will stay in excellent condition.
Use a towel that is fully saturated with acetone to rub the plywood.
Its crucial to let the acetone dry for a few hours before applying a layer of waterproof sealant to make sure that it wont affect its properties.
You can also use water to clean plywood perfectly. Use a piece of cloth to clean the wood and remove any remaining debris.
You should let the wood dry completely before applying a sealant.
Waterproof Plywood Deck / Floor
The deck is an integral part of many houses, and it needs to be waterproofed. Some decks look clean and waterproof, while others look messy. Exposed wood is the cause of this. The waterproof deck is a bit harder. Well, there are so many choices to make your deck waterproof, just like any other home improvement products.
There are many waterproof wood sealers, but many of them might fail. In this guess, I am suggesting you use a liquid rubber waterproofing system. It ossifies the plywood deck and protects your deck. Choose the best one from the market.
Now, you must want to know about the process of waterproofing a deck. Well, follow the process below.
First, clean the surface and wipe it with a dry cloth if the surface is dry to make the surface dry and clean. After cleaning, take a suitable liquid rubber waterproofing. Then, apply a coat of the liquid rubber waterproofing and wait for at least 24 hours. Apply 2 to 4 coats of this. The number of coats is depended on the application.
Here I am suggesting you some tips which will make it easier for you. Make sure that the surface is clean, as dust can cause loss of adhesion. Also, you can apply it by using a brush or roller. It will smoothen the application. A paint sprayer also can be used.
Keep In Mind:
Final Words:
You can use spray on or paint on waterproofing as it is used widely because of its easiness and good quality.
M Reinforced Polyurethane Foam Boards
3M has developed an alternative to marine plywood. They call it 3M Reinforced Polyurethane Foam boards. It is a rot-resistant and lightweight material that can be used in semi-structural and structural constructions.
The foam boards are reinforced with fiberglass so they can be used in marine applications. This material offers weight savings that range from 30% to 60% compared to conventional plywood. This makes it one of the best marine plywood alternatives.
These foam boards are available in different weights. The lightest is 15 pounds per cubic foot, and the heaviest is 28 pounds per cubic foot. They are also available in sheets or boards measuring 4 feet by 8 feet.
These sheets are perfectly straight and level. They are easy to work with, and they do not tend to warp. Conventional plywood is prone to chipping and warping. There are no such tendencies with these 3M foam boards.
There are certain advantages to using these reinforced polyurethane boards. They are resistant to rotting. These boards also provide better adhesion compared to ordinary wood because their moisture content is very low.
Also Check: Is Boat Insurance Required In Minnesota
How Does One Waterproof Marine Plywood
The type of wood that the marine plywood consists of determines the best way to waterproof the wood. For example, one might be using Douglas-Fir to build the main hull due to its lower cost than woods like teak.
However, as was just discussed, fir tends to crack when exposed to the sun and weather. This type of wood is an excellent builder grade marine plywood. Moreover, it requires being coated in a substance such as fiberglass epoxy to achieve a waterproof seal.
Moreover, if exposed to water, fir plywood, even marine-grade, will break down.
More expensive and higher quality marine plywoods may not require something as drastic as fiberglass skin. However, sealing all marine woods is a necessity.
For the higher quality marine plywoods, the sealing process typically involves multiple layers of epoxy applied to the wood to achieve waterproofing qualities.
More Than Boats For Marine Plywood?
Is marine plywood only for boat building?
Any time a dock requires some side or roof panels, using plywood, such as marine-grade plywood, is smart.
So What Are We Paying For
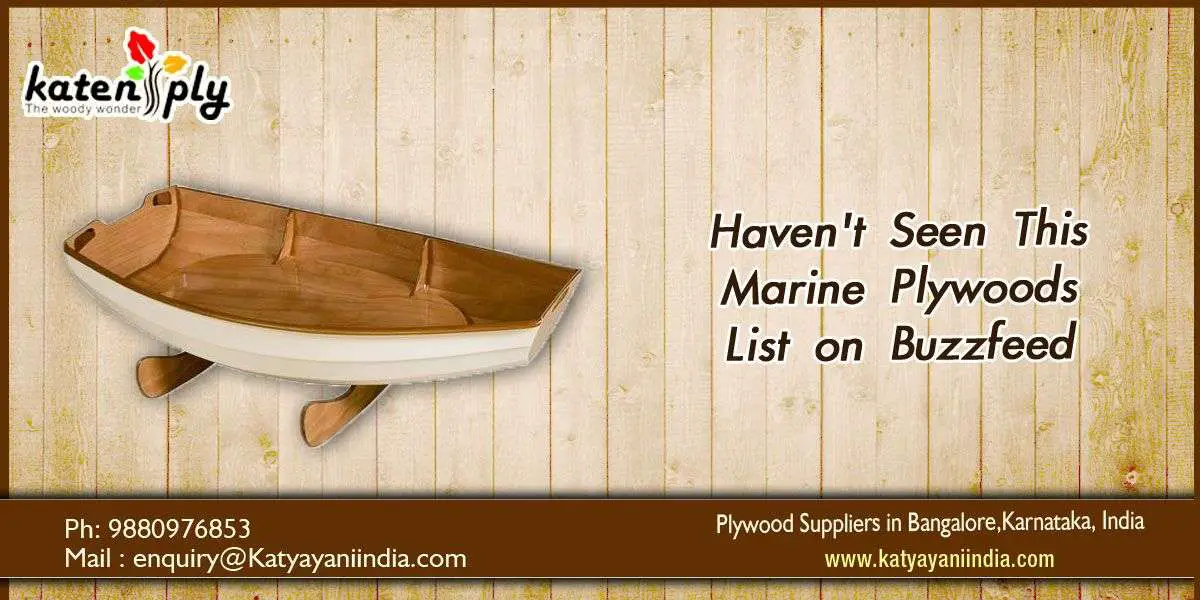
BS1088 is the British Standard specification for that applies to plywood produced with untreated tropical hardwood veneers that have a set level of resistance to fungal attack. The plies are bonded with Weather Boil-Proof glue.
Illustration 1
Although this stamp is said to be the seal of approval, there have been various arguments over the years regarding the quality variance. A reader submitted a photo of a piece of so-called marine plywood that he recently purchased. It can be seen above the Illustration 1caption. Dont worry there are some ways to test the quality of your plywood :
- Cut some small samples and leave them in the dishwasher for a few cycles.
- Simmer samples in hot water for a few days to see if they delaminate.
With these factors now in mind, it is possible to find cheaper alternatives and more importantly available alternatives. Its all good and well only wanting to use marine plywood but if none of your local building supply stores sell it, then you wont get very far!
Read Also: Who Owns Freedom Boat Club
How To Waterproof Wood For A Boat
As mentioned above the boat is made up of marine plywood which is different from ordinary plywood. It can have up to 10 layers of thickness whereas regular plywood only has 3-5 layers. Although marine plywood can survive the marine environment waterproofing, it will help in increasing its longevity. There are many ways to waterproof the boat, but I would recommend using a wooden sealant for waterproofing the plywood for the boat. There are many branded sealants available in the market that are made for especially waterproofing the boat. You can select one of your choices
1.Use a Sandpaper for prepping the surface for sealing
This step is similar to the step in painting the boat. It is always recommended to sand the surface down before starting to apply any paint, wax or a seal. Start sanding the surface area of the boat with the help of sandpaper. I would recommend using 80-grit sandpaper. Go over all the surfaces and make sure the surface is ready to apply a seal.
2.Clean the area thoroughly
Once you are done sanding the plywood, you can clean it with a cloth or even wash it for making sure that there are no debris or strains on the boat. In case you hose it down for washing take a cloth and let it dry before you start applying a seal.
3.Start sealing the plywood with the help of a brush or sprayer
4.Add more layers of sealant
Good Plywood Is Different
Even though the plywood products sold by most hardware stores are graded A, B. C. and D , they aren’t considered as high quality as marine and other types of quality hardwood plywood. Standard plywood is made with fewer, thicker layers and mostly contains softwood, like pine or Douglas fir. The interior layers also have voids, or holes, that you can’t see until you cut into the plywood panel. Marine plywood is a type of hardwood plywood. True hardwood plywood is made with thin layers of 100 percent hardwood, which generally is stronger and harder and has a finer grain than softwood.
Plywood sold as “void-free” does not have voids hidden in the wood layers. As for the layers, a lot of thin layers is better than fewer thicker layers because thinner results in a stronger, denser panel with edges that cut and sand cleaner.
You May Like: How To Get Mold Stains Out Of Boat Seats
How Is Plywood Made
If you are wondering how the name plywood came to be, we would love to enlighten you. When you are referring to the different pieces that are glued together, they are called the ply. Once all of the hundreds of layers of ply are adhered to and compacted together, you will eventually be left with something that resembles a board of wood. This is plywood. The last step of the process of making plywood boards is when it is treated with a bit of heat, but not too much to make the glue meet before it can be set properly. Once this is complete, the plywood can be cut to shape and used for whatever you will.
Is It Necessary To Seal Marine Plywood
all sides and edges
Okoume MahoganyMarine Plywood |
Okoume also known as gaboon or combogala, is only found in Gabon, the Congo and Equatorial Guinea in Africa. Okoume has a very high strength to weight ration which is why it is the plywood of choice for racing boats and applications where weight is important. It has a specific gravity of .43 and averages 27 pounds per cubic foot. The main drawback of Okoume is that it has no rot resistance. Therefore it is very important that all edges and faces are thoroughly sealed with epoxy and varnish to keep water from penetrating into the plywood. Okoume grows rapidly and regenerates well in clearings which makes it a very renuable.Okoume is light pink in color with a variable interlocked grain. The panels are normally painted or finished bright. |
Read Also: Resale Value Of Pontoon Boats
Contact Curtis Lumber & Plywood For More Information
Curits Lumber & Plywood is an independently-owned-and-operated wholesale lumber distributor that has specialized in both plywood and pressure-treated products since our founding in 1957. We also offer Marine-Grade Plywood in many different sizes.
Curtis boasts a large fleet of delivery trucks that lets us efficiently serve retail lumber dealers throughout the Mid-Atlantic Region. Our employees are highly knowledgeable about all of our products and we answer our own phones. We are able to furnish direct trailer load shipments or can pull orders to the piece for special projects.
Curtis will always work hard to find any item you need, even if we dont have it in stock. Call Curtis Lumber & Plywood today at 972-1947 or contact us online for more information about our products. Youll hardly find a more reliable wholesale lumber distributor in Northern Virginia.
Know What Type Of Wood You’re Working With
Not all wood will require treatment. For instance, marine plywood should be good enough at fending off water damage on its own without the need for extra treatment. If you’re using regular plywood, the general rule is that the thicker it is, the more layers of sealant you’ll need. Don’t be afraid to ask a professional to find out how many coats you should apply on your specific plywood.
Read Also: How Do I Register My Boat In Colorado
How You Can Waterproof Ordinary Plywood
One affordable alternative to marine grade plywood is by using ordinary plywood and making it waterproof. You can do this because all plywood, including the marine type, are made with the same adhesive, Type A Phenolic Bond glue line EO formaldehyde rating. This glue securely bonds the core and the ply veneer sheets together.
The quality of the glue line determines the degree to which birch plywood and marine plywood can resist moisture. All the edges of the plywood board must be protected and sealed by layers of oil/wax products, sealant, or water repellent varnish.
Thus, if you really want to use ordinary plywood for marine applications, all you need to do is to use good quality ordinary plywood. And then research the proper method of waterproofing it. Buy the required materials and follow the legitimate instructions on how to properly waterproof that plywood sheet.
Cover All Edges And Sides
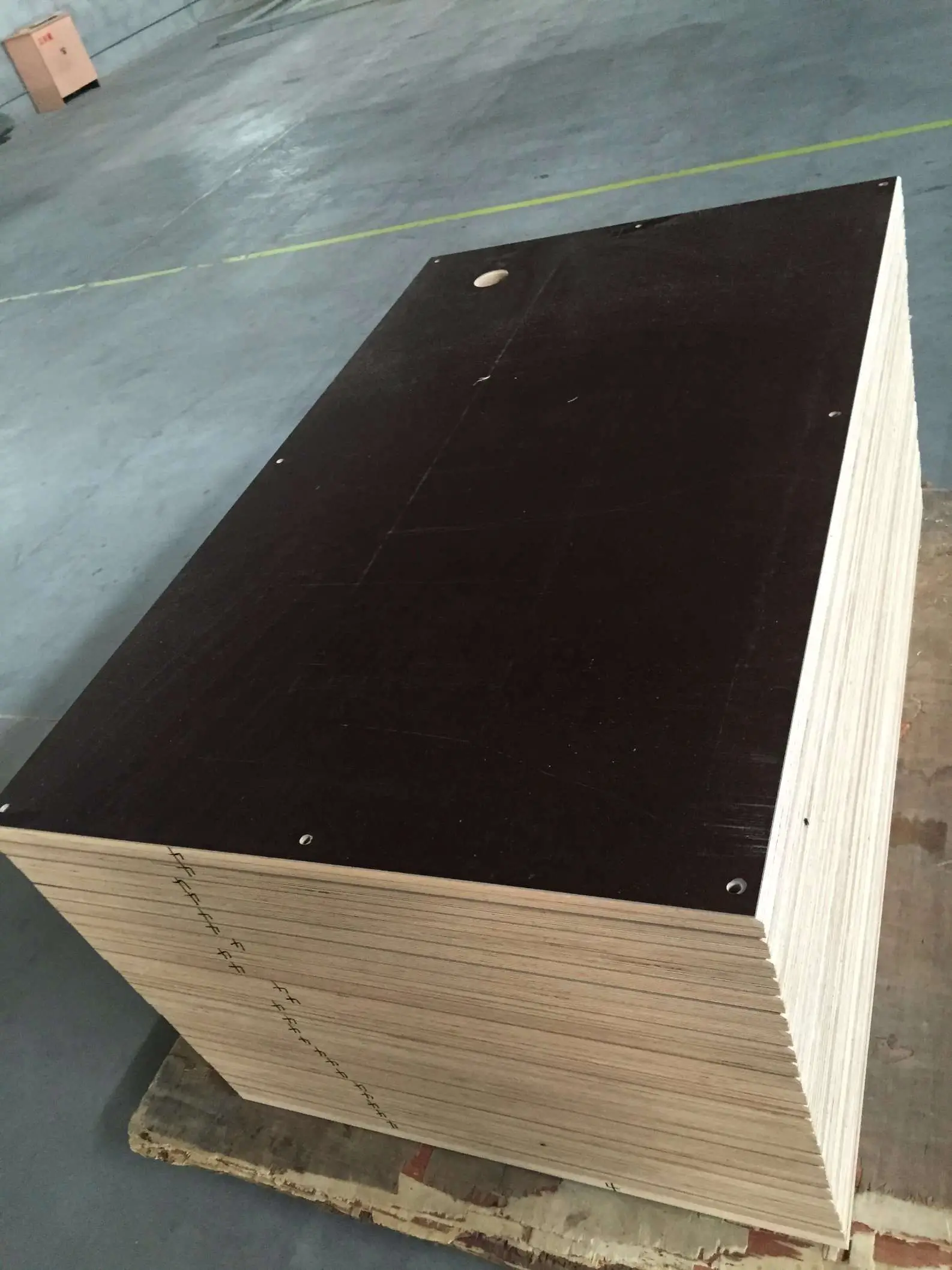
Leaving even the smallest surface of your plywood untreated leaves it vulnerable to water penetration. It’s always best to apply sealant to a boat plywood piece while it’s not installed on the boat so you can thoroughly get all of the exposed sides and edges of the whole plywood. See to it that the sealant soaks through the ends of the plywood where water damage typically starts. That’s also why sanding is especially important.
Also Check: How Do I Register My Boat In Colorado
How To Waterproof Wood For A Boat Guide For Waterproofing Plywood
If you are someone who owns a boat you probably know how important it is to waterproof the plywood of the boat. The plywood that is used in the making of the boat is generally marine plywood which can sustain in water. However, it is necessary to waterproof it so that it is not damaged by being in constant contact with water. The plywood might be damaged if it is not waterproofed correctly. Apart from water UV rays also damage the plywood, and hence it becomes vital to waterproof it. To make the entire process of waterproofing easy, I am going to list the procedure step-by-step along with some tips and tricks in this article.
How To Waterproof Plywood With Pva
Besides the regular waterproof paint, you can opt for PVA . It easily adheres to the plywood surface, forming an effective waterproof film.
As already discussed above, waterproof paint is made with a latex element. On the other hand, PVA is a water-soluble synthetic polymer. So, whats the difference?
In terms of quality, both are equally efficient. However, its recommended to apply PVA to indoor plywood as it can easily get washed away with water or rain.
Unlike the regular waterproof paint, you only need to apply three coats of undiluted PVA. Just ensure the previous coat dries up completely before applying the next one.
Read Also: What Must Be Affixed To Both Sides Of The Bow Of A Vessel
How To Seal Plywood Edges
Because plywood is made of several thin layers, the edges are very vulnerable to water. Generally the surface of plywood is naturally water resistant, but the edges absorb moisture like a sponge.
When water is absorbed into the plywood edge it can damage the wood much faster. The edges are an easy way for water to get directly in between the plywood veneer sheets. For this reason its very important to seal and waterproof them.
Sealing plywood edges is very simple,
- Apply several coats of waterproofing with a brush. Edges will soak up more sealant than the surface so youll need more per inch.
- Allow each coat to dry before you apply the next.
- The edges will soak up the varnish quickly so use several coats.
- Its OK to go thicker around the edges.
- Watch for and clean up drips.
- You can use a roller on the edges too but it will drip easier. A brush is your best bet.
How To Waterproof Plywood: Steps To Protect Plywood Boat &
1/6/2019·To make the plywood of the boat waterproof follow the below given steps: Clean the sides of the veneered marine boat with a clean cloth. Jolt epoxy with glue and open lid then mix epoxy and hardener in a bowl. Next step is to take a paintbrush and fill all the holes and joints with epoxy. Wait for three hours and then apply a second coat.
You May Like: Does Banana Boat Test On Animals
What To Look For In A Marine Plywood
When purchasing marine plywood, there are several things to watch for in the quality of the wood. First, the board should be solid, with no layer delamination of any kind. Also, watch for any holes or loose knots there should be none. If there are loose knots or holes, the quality is poor even in a single outer veneer. Remember that any hole or loose knot could allow water to seep in between the layers.
If fir is the plywood of choice, check for cracks or checking as they are also known. It can mean the plywood has been outside, exposed to the elements for some time.
If one uses fir plywood, it will require a layer of fiberglass and resin to prevent leaking.
Cover Your Marine Plywood With A Coat
Generally, when sealing or even painting plywood youll only be applying your coats to a single side. This makes sense as most times a single side will be the one that is exposed and therefore its unnecessary and often a bit of a waste to cover the whole thing. However, because we want to ensure that we wont have any problems dealing with water and other weather elements we want to seal the entire sheet so we dont have any deterioration problems down the line. For doing this youre going to want to use a foam brush with some clear, penetrating epoxy. Make sure you saturate the brush and then start spreading the epoxy on the top and side edges, as well as one of the faces dont do the bottom edge, otherwise, you wont be able to allow it to stand and dry! Once its all dry youre free to move onto covering the bottom edge and the other side of your Marine Plywood.
You might be wondering why use a clear, penetrating epoxy sealer? Well, the reason is that this sealant is transparent and drives itself deep int your sheet of ply rather than sitting on the surface. Youll also find that with this sealer you will require less maintenance, as other sealers require more coats and generally need to be reapplied every few years to continue working at the same level of protection.
You May Like: Hydrofin Pontoon