Some Considerations On Changing From Steel To Aluminum
Aluminum is not as strong as steel so some compensations must be made if using it in place of steel. Without getting too technical, with aluminum used for shell plating compared to mild steel, yield strength for aluminum as-welded is about 25% to 35% less than that of steel. In addition, it has about 75% the tensile strength at 1/3 the weight. Put another way, to get the same strength as steel in an aluminum hull, it needs to be approximately half the weight of steel.
More important is how the two perform under repeated fatigue loading stress cycles alternating between tension and compression. Tests show that for a similar number of cycles, steel stays above its yield strength threshold. But aluminum dips below it, suffering a loss so that strength is equivalent to only 75% of its yield stress. In other words, it is more likely to fail due to fatigue over time, an important consideration for boats subject to such conditions . The point is that if you decide to adapt a steel design to aluminum, you’ll need to increase scantlings . But by how much?
Creating The Initial Folds
Tip: When you go to fold the second side, use the first fold as a reference point.
Plywood Jon Boat Theplywoodcom
As this blog mentions, many would-be boatbuilders are put off trying because, unlike lots of other woodworking jobs, building a boat requires many extra skills that some hobbyist woodworkers dont possess. However, if you choose a simple project to start with and you have the right plans to follow its a perfectly achievable task. And if you think that sounds like something you want to try, this post teaches you everything you need to know.
Recommended Reading: How Much Are Boat Club Memberships
Tips On Being A Resourceful Builder
If working from stock plans for an aluminum boat, the designer probably specified certain sizes, types, and alloys of members for framing, etc. However, its possible that not every item will be available from your supplier or at a reasonable price. But deviations may be possible. Most designs have some latitude in alternates that can be substituted. Its simply not practical for a designer to specify each and every option.
For example, angles can be substituted for tee’s and vice versa. Channels can be made from split square or rectangular tubing, or even split pipe if somewhat larger than the specified channel. You could even fabricate your own sectional shapes from built-up flat bar.
Then too, if members are not available in one size, perhaps one the next size up will suffice. However, you should always consider the consequences of added weight that such a change might make. Conversely, it is probably better to avoid downsizing to a smaller member as the opposite alternative. But you may compensate for using smaller members by placing them closer together, for example, in the case of longitudinal stiffeners, and/or you might space frames more closely together all in an effort to reduce the area of unsupported plating.
Jon Boat Design Boatdesignscom
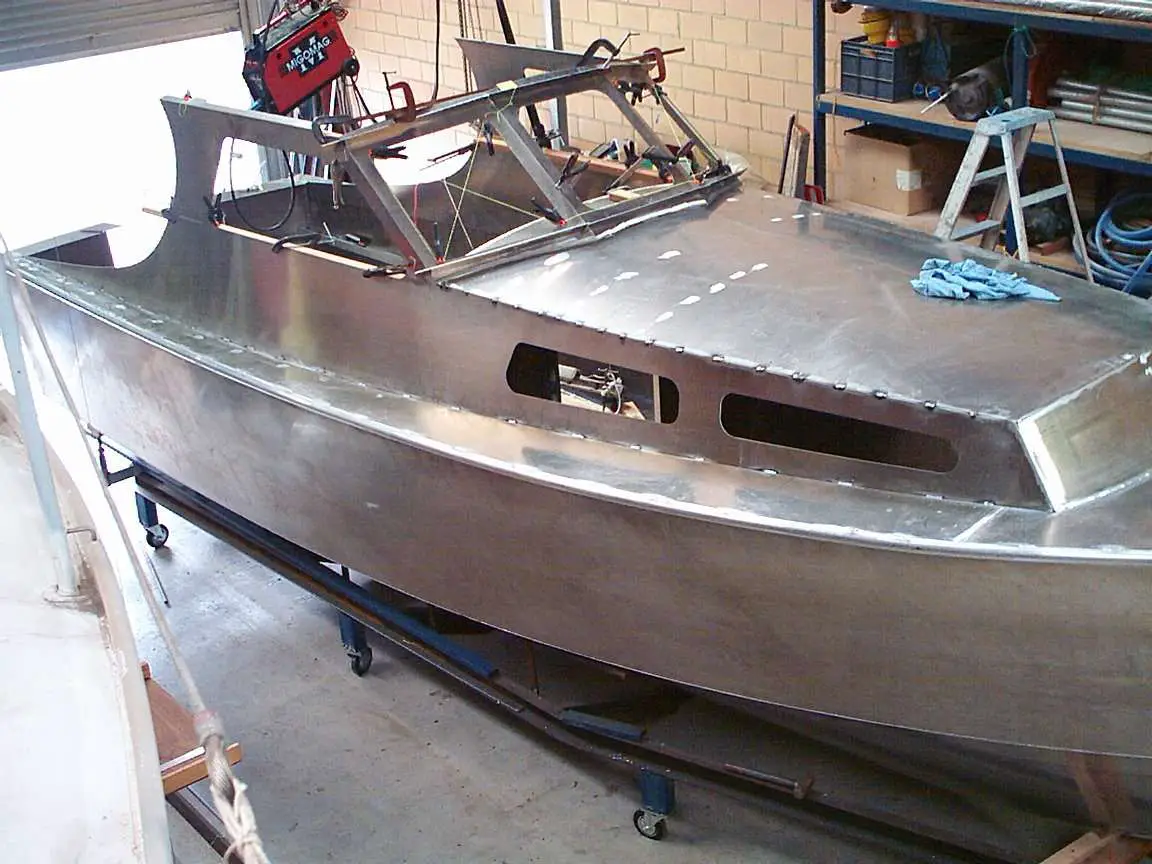
If youre not sure about building a boat from scratch, it might be a better idea to think about buying plans and a kit. That way, you can be sure that the boat you build will be everything you hoped for when you finish. If that sounds interesting, heres a page that should be of interest since it gives you an introduction to just such a project.
Recommended Reading: Banana Boat Cruelty-free
Framed Boat Advantages For Do
Using a frame substructure for setting up your hull has several advantages for the do-it-yourselfer typically working alone. First the frame substructure makes it easy to assure hull accuracy that is so important to ultimate performance in a powerboat. Second, the framework makes it possible to build from “off-the-shelf” materials and shapes available anywhere for lower costs and easier material purchasing. Finally, the framework makes it easier to form hull members in place and during weld-up since clamps and other devices can be readily used most anywhere as required, acting as extra pairs of “helping hands” in the process.
Factory production boatbuilders often use specialized forming equipment not always available to amateurs, or use forming services that might be provided by metal suppliers when quantity requirements are high. For example, special rolling and/or bending equipment might be used to form integral shapes in hull plates for stiffness, etc.
Conversely, a design for the do-it-yourself builder would more likely specify internal longitudinal stiffeners , and be designed in such a way so that no special forming or bending equipment or outside services are required. Either method gets the job done but the latter is easier and cheaper for most building their own boats.
See What Recent Buyers Have To Say
My H24 Bay is a haus! I love the dual live wells because I do a lot of live bait fishing. They keep fish and bait alive all day and are plenty big enough to accommodate the limit of fish. There is plenty of room for passengers and gear. Finally, I love the way the boat rides and handles. It turns on a dime, gets up on plane in little to no water, can be trimmed out while running wide open, and never bounces. I bought the boat from Marshall Marine, which went very smoothly. Great job Xpress!
Nick B.
The top three features that I like most about my X21Pro are the SeaDek that allows me to fish barefoot all summer long, the Hyper-Lift hull the provides tremendous speed and agility, and the storage compartments that allow me to store a maximum amount of tackle, rods, and equipment, which is very helpful for tournament fishing. I have never owned a bass boat with as much storage! My buying process with Carey and Sons Marine, near Dallas, TX, was fantastic!
Ethan C.Brad B.Randy N.Larry S.Brett K.Keith D.Preston L.Cody N.Darren H.Cameron O.Daniel R.Tim D.Phillip I.Tony C.Paul J.Jake B.Dallas W.Matt M.
I own a 2012 XP180. I love the ride for a flat bottom. I fish the Chesapeake Bay, especially in the fall for rockfish lol. The storage is perfect.. whether I am fishing, crabbing, or hunting. The camo design is different and stands out. I bought the boat from R & C Marine in Queenstown, MD. Good guys. They even came out to replace the locks.
Sam T.Brandon D.
Don’t Miss: How To Get Rid Of Mildew On Boat Seats
Pro Tips To Save You Money On Your Next Aluminum Boat Build
There are 4 major costs involved in building an aluminum boat from design to construction: design, cutting, shipping, and building. As the saying goes time is money and the ability to work efficiently in each step of the build process will save you money and make the boat building experience a more enjoyable process.
Reducing the Cost of Your Aluminum Boat Build
What are some ways that you can reduce the costs associated with aluminum boat building?
Tech Tips And Practical Info For Doing It Yourself
The number of people with aluminum welding skills and access to fabricating equipment has increased considerably over the years. Yet many are unaware of fundamental considerations confronting the short-handed amateur building a single boat for his own account. Ill discuss many of the more common issues, especially as they relate to powerboats in the 15′ to 40′ size range we most commonly deal with today.
You May Like: Best Outboard Bowrider
One Sheet Jon Boat: 20 Steps Instructables
The boat in this plan is the result of a great story. As this DIYer tells us, in his town, there is a contest to build boats using very limited materials, mainly consisting of one sheet of plywood. The big advantage of that is that any boat you make is sure to be extremely inexpensive, and if you want to know how he did it, this tutorial gives you a clear step-by-step guide along with plenty of photos to show you what to do.
Thicker Versus Thinner Framing And Plating
There is an on-going debate as to whether welded aluminum boats should be made as light as possible via light plating and framing , or with heavier plating using minimal but also somewhat huskier framing members. To put this issue in perspective, well assume strength is sufficient in both cases in order to examine the merits otherwise.
A boat built with light plating and framing is lighter in weight for more-economical operation, has a higher speed for a given power, is more-easily trailered, has greater payload, and because it has less material, will cost less.
Advocates of heavier plating and framing counter that thicker plating is stiffer which better resists flexing, twist, and fatigue, won’t dent as easily, and will deter longer any effects of corrosion. They also claim that lighter scantlings take more time and labor to build , and that any increase in weight and/or cost is offset by a reduction in framing. Then too, they claim thicker plating is less prone to distortion by welding heat and it’s easier to make stronger joints since it’s more likely that both sides of joints can be welded without problems or defects. In addition, thicker members are often easier to handle and work since they resist distortion and are not so “floppy”.
Also Check: How Much Is A Freedom Boat Club Membership
Homemade Wooden Jon Boat Build From Robert Heffner
In this video, we get to watch as a high-quality Jon boat takes shape, right from the beginning up to the point when it was taken out onto the water for the first time. This YouTuber offers detailed plans for this boat for sale, so if you want to make something similar, you might consider buying them and copying what he did.
Homemade Wooden Jon Boat
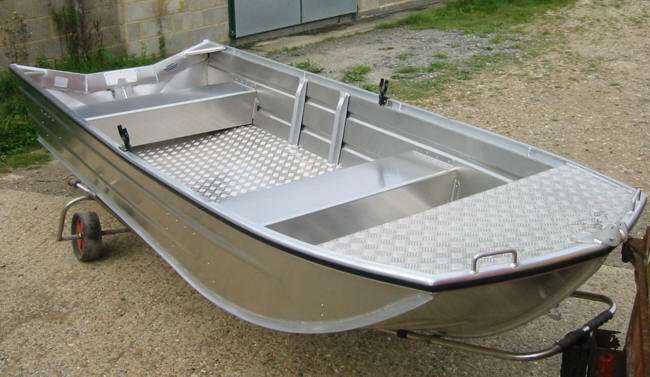
If youre thinking about making a Jon boat of your own and are wondering what the job is likely to entail, this video should be of interest. In it, you get to see how the project went from beginning to end, and as you can see when its done, it looks like it turned out pretty well. Were impressed!
Recommended Reading: How To Clean Vinyl Boat Seats Of Mildew
Homemade Jon Boat Build From Dooryard Fabrication
This is the first video in a series detailing a complete Jon boat build using aluminum. In the first video, you get to see how they measured and cut the hull. Its a little lacking in explanations, but if you have the necessary skills, youll probably be able to work it out anyway. And to find out how the boat looked when it was finished, you can check out the rest of their videos too.
Thicker Versus Thinner Framing And Plating Whats Best
There is an on-going debate as to whether welded aluminum boats should be made as light as possible via light plating and framing , or with heavier plating using minimal but also somewhat huskier framing members. To put this issue in perspective, weâll assume strength is sufficient in both cases in order to examine the merits otherwise.
A boat built with light plating and framing is lighter in weight for more-economical operation, has a higher speed for a given power, is more-easily trailered, has greater payload, and because it has less material, will cost less.
Advocates of heavier plating and framing counter that thicker plating is stiffer which better resists flexing, twist, and fatigue, wont dent as easily, and will deter longer any effects of corrosion. They also claim that lighter scantlings take more time and labor to build , and that any increase in weight and/or cost is offset by a reduction in framing. Then too, they claim thicker plating is less prone to distortion by welding heat and its easier to make stronger joints since its more likely that both sides of joints can be welded without problems or defects. In addition, thicker members are often easier to handle and work since they resist distortion and are not so floppy.
Read Also: How To Clean Boat Canopy
Duckworks A Lightweight Jon Boat
In this post, this blogger takes us through how he ended up making himself a simple Jon Boat. Finding that with age, he was no longer able to paddle like he once could, he decided he wanted to try a powerboat but he also didnt want to spend lots of money. Instead, he decided to build his own, and this tutorial will allow you to copy his ideas.
Aluminum Boats Are Built For Life
The Coastal Craft 33 Profish is built entirely of durable, rugged aluminum, yet weighs only 11,000 pounds.
In the fiberglass-centric world of recreational boating, its easy to forget that some of the finest yachts are built of welded aluminum. So are many commercial small craftbelow 100 feetin operation today, as well as ships to more than 300 feet, where reducing weight to achieve high speeds is very important.
First, a science lesson. Manufactured from the ore bauxite, aluminum is a silvery-white, ductile metal with excellent corrosion resistance, strength and toughness. It can be easily cast and welded, melts at 1,220 degrees , and weighs 170 pounds per cubic foota little more than a third as much as steel. Aluminums strength varies depending on the alloy, but marine-grade 5083 H-32 aluminum plate starts to deform at 34,000 psi and fails at 45,000 psi.
What this means for the boat owner who runs aground at 25 knots is that the metal stretches and dents before it ruptures, which is good when the goal is keeping the ocean outside the boat. In fact, aluminums ductility lets it deform, or stretch, some 25 percent before it fails, and this plastic region is one of the characteristics that make it so suitable for boatbuilding.
Commercial companies love aluminum boats for their ability to withstand punishment every time they are put to work.
With all that in mind, here are several things to consider when talking about aluminum boats.
Also Check: Freedom Boat Club Reservation
Homemade Jon Boat Plans You Can Diy Easily
Jon boats feature an extremely simple design, and their flat bottom makes them suitable for use on even shallow water, so theyre a popular choice with anglers and many other inland boat users.
Theyre also extremely easy to build, so to help anyone who wants to try, weve had a look online to see what other people have been trying and as a result, here are 27 great DIY Jon boat plans you can have a go at recreating at home.
From Stem To Stern Every Inch Of A Legendcraft Is Custom Built Tough
How to build an aluminum boat hull. 14 ft orca loa: Looking for an aluminum houseboat hull manufacturer, builder, or shop to fabricate a custom aluminum hull? Save $1000s by building your dream boat with only a few tools and a little sweat equity.
As with any material, it costs more to build an aluminum boat thats light and strong. Add pennies until the boat sinks. 97 best aluminum boat ideas images in 2018 aluminium boats.
Aluminum boats using welded marine alloy construction are strong, lightweight, durable, and easy to maintain. And just by using more of it, aluminum can produce a vessel thats stronger than steel at less weight. Ground to hull on aluminum boat?
13′ 9 / 4.19 m. Most often used to build boat hulls due to stress corrosion cracking resistance. Since then, lowe has created generations of family memories through great experiences on the water and has developed a reputation for building high quality, yet affordable aluminum boats and pontoons to suit almost any need.
Boat builders use the incremental backstep process. I am using 1/4 inch aluminum for the hull and a bit concerned about being able to bend it into shape. I need to find an experienced fabricator to build an all aluminum hull about 34′ long with gently curved bottom, sides and roof that i can haul home on a custom trailer to finish myself.
Here’s a simple but good little fuse block, buss bar combo. We are your one stop shop for customizable aluminum boat kits. Best alloy for salt water.
Also Check: Banana Boat Cruelty Free